Nelle varie realtà produttive, così come in quella tessile, l'efficientamento energetico è una priorità fondamentale per le aziende che cercano di ridurre i costi operativi e l'impatto ambientale.
L'utilizzo dell'aria compressa rappresenta una risorsa preziosa per migliorare l'efficienza energetica nei processi tessili e grazie agli avanzamenti tecnologici, è possibile avvalersi di sistemi di aria compressa sempre più efficienti e sostenibili che consentono alle aziende tessili di ottimizzare i propri processi produttivi e ridurre i consumi energetici.
Per questo vogliamo presentare la nuova case history di successo Kaeser Compressori per la storica azienda Gaspare Sironi S.p.A
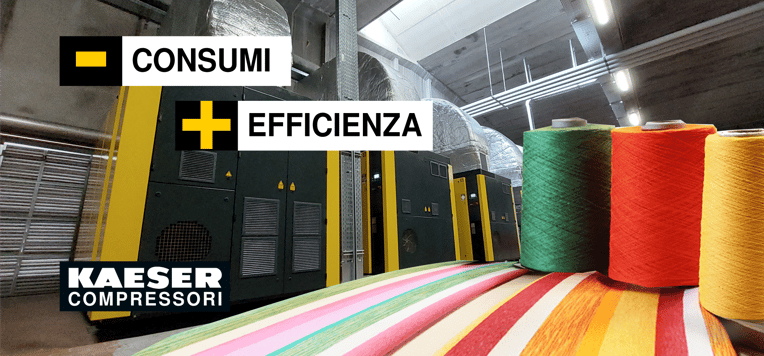
Leggi anche: Servizio locale per le PMI
Leggi anche: La bassa pressione nel Food & Beverage
Leggi anche: Qualità e sicurezza al 100% con Kaeser Service
Compressori Kaeser: risparmio energetico e manutenzione predittiva con SAM 4.0
Due compressori modello DSD 240 con potenza nominale da 132 kW, tre compressori modello DSDX 305 da 160 kW di cui uno è dotato di inverter.
Per il trattamento aria sono stati installati quattro essiccatori a massa termica, raffreddati ad aria modello Secotec TG960, 4 filtri a coalescenza KS700 dotate di manometri differenziali e 5 valvole automatiche DHS 150 per il controllo del flusso e della qualità dell'aria.
Lo studio di fattibilità del progetto ha richiesto molto tempo e l'interazione tra i diversi dipartimenti di Kaeser Compressori.
Il dipartimento Application di Kaeser Compressori è stato coinvolto nel progetto sin dal primo momento infatti alla base del processo di analisi e progettazione degli impianti ci sono le rilevazioni dell'impiego di aria compressa per le esigenze del cliente.
Per la rilevazione dei dati sono stati utilizzati strumenti di misura accurati, i dati vengono poi elaborati da programmi avanzati tenendo conto dei parametri fondamentali delle reti di aria compressa.
ADA-KESS per i ridurre i consumi di energia
Portata d'aria, pressione di impianto e consumi energetici sono le variabili che tramite il nostro software esclusivo ADA (AIR Demand Analysis) ci permettono di identificare e valutare le caratteristiche uniche di ciascun impianto.
Con il nostro software KESS (Kaeser Energy Saving System) possiamo simulare il comportamento di una nuova sala compressori sul profilo dei consumi del cliente, registrato durante un periodo di produzione significativo.
La soluzione Kaeser che abbina qualità, efficienza e risparmio energetico
Grazie al proprio Know-how Kaeser è stata in grado di costruire una scenario virtuale di lavoro, simulando il funzionamento dell'intero impianto per verificarne le potenzialità rispetto alla domanda d’aria compressa.
Proiettando questo profilo su base annuale il sistema è stato correttamente dimensionato, scegliendo i componenti più adeguati ed identificando potenziali risparmi delle diverse soluzioni.
Oltre alla corretta selezione dei compressori si è lavorato molto per garantire che anche il trattamento aria fosse efficace ed efficiente. L’impiego di essiccatori con circuito frigorifero a massa termica, filtri a coalescenza, tubazioni e valvole di stazionamento automatico garantisce un costante mantenimento in sicurezza dell'impianto.
È stato elaborato un layout 3D personalizzato che ha reso possibile valutare gli spazi e la ventilazione e la corretta installazione dei macchinari.
Il risultato di questo lavoro è confermato non solo dai sistemi di monitoraggio Kaeser ma verrà certificato anche dal G.S.E. con l'emissione di titoli di efficienza energetica.
Il passaggio del vecchio impianto oil free al nuovo con compressore a vite lubrificato ha portato notevoli vantaggi.
Il frazionamento della potenza totale su più macchine consente una soluzione più flessibile che è in grado di rispondere adeguatamente alle variazioni produttive, di ridurre i consumi elettrici e quindi le emissioni di CO2.
1.L’effettivo raggiungimento delle classi di qualità dell'aria desiderata in accordo alla ISO 85731 per il corretto funzionamento dei telai
2. l'abbattimento drastico dei consumi di gas metano per il riscaldamento dello stabilimento grazie al recupero del calore in esubero dei compressori
3. la netta riduzione dell'impatto acustico ambientale grazie all'impiego di macchine particolarmente silenziose
4. l'azzeramento dei consumi d'acqua e degli additivi chimici grazie all'impiego di macchine raffreddate ad aria
5.la riduzione dell'impatto ambientale anche grazie alla scelta di essiccatori Secotec che impiegano gas refrigerante r513a con basso Global Warming Potential (GWP).
6.L'analisi costi benefici degli interventi eseguiti ha messo in evidenza che la riqualificazione energetica della sala compressori ha portato ad un efficientamento di circa il 25% e ad un veloce tempo di ritorno di investimento.
Kaeser Compressori si conferma partner affidabile per la realizzazione di impianti che garantiscono più aria compressa con meno energia.
Lascia un commento