Nel corso dell'articolo precedente abbiamo preso in esame il caso di TMB S.p.A., un'azienda con 60 anni di esperienza alle spalle, specializzata nella lavorazione di componenti nelle leghe di alluminio, per una clientela diversificata, nei settori industriali della meccanica di precisione.
Una realtà altamente competitiva nel comparto del processo produttivo e che recentemente ha deciso di sviluppare, grazie alla competenza di Kaeser nel campo delle soluzioni tecnologicamente all'avanguardia relative all’aria compressa, un progetto di efficientamento energetico per la produzione e il trattamento dell’aria compressa per ciascuno dei 4 locali compressori presenti all'interno del proprio stabilimento.
Il revamping degli impianti e locali compressori
La caratteristica più forte e importante di questo progetto, nel suo insieme, è stata la volontà di rifare completamente ogni singolo locale-compressori.
Questo ha significato:
- rimozione dei prodotti esistenti,
- rifacimento delle tubazioni,
- inserimento di nuovi prodotti e messa in servizio delle macchine.
Il tutto senza arrecare alcun deficit alla produzione.
Cronoprogramma delle attività
Ogni singola fase del progetto, esteso a tutti i locali compressori, doveva essere programmata nel dettaglio, per consentire l’esecuzione dei lavori senza interferenze tra le varie maestranze e, soprattutto, per garantire la fornitura di aria al comparto produttivo senza fermi impianto.
Sviluppo del progetto in 3D
Per riuscire a definire, fin dalla fase iniziale del progetto, gli spazi e gli ingombri per ospitare le nuove macchine è stata richiesta la progettazione mediante disegni in 3D.
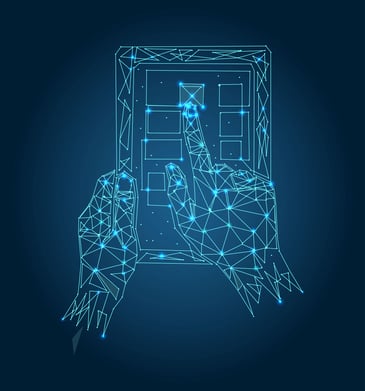
Le fasi di esecuzione del progetto di revamping
Chiariti gli obiettivi del progetto e definito un cronoprogramma delle attività principali, oltre alla sequenza temporale di ottimizzazione dei locali compressori del polo industriale di Ceregnano, si è deciso di schedulare le attività utilizzando in sequenza le 6 fasi di seguito elencate.
Prima fase
Viene effettuata una misura diretta (con durata di 15 giorni consecutivi e intervallo di 5 secondi tra due misure successive ndr) delle principali grandezze caratteristiche del processo di produzione dell’aria compressa, quali: portata, pressione, potenza assorbita da ogni singola unità, punto di rugiada in pressione a valle del trattamento.
Seconda fase
A fronte dei “dati di progetto” ricavati dalla fase precedente, si simulano delle soluzioni che vadano ad ottimizzare la situazione in funzione degli “obiettivi del progetto”, tenendo in considerazione i “profili di portata” registrati e le possibili variazioni nel corso degli anni a venire.
Terza fase
Al confronto con la Direzione di TMB S.p.A. sulle diverse soluzioni proposte, si è ricavata la configurazione che meglio soddisfa lo stato dell’arte e le possibili esigenze future.
A questo punto, è stato sviluppato il modello 3D per poter individuare la migliore disposizione dei prodotti a fronte di uno spazio ben definito.
Quarta fase
Successivamente alla selezione dei prodotti per la produzione e il trattamento dell’aria compressa, sono stati effettuati il dimensionamento e l’installazione delle tubazioni nel locale compressori, volti ad ottenere i valori minimi di perdita di carico localizzata e distribuita.
Calcolatore della perdita di carico nelle tubazioni
Quinta fase
Il posizionamento e il collegamento dei singoli prodotti sono risultati semplici ed efficaci grazie al progetto 3D.
Si è, quindi, proceduto al collegamento e alla configurazione della centralina di supervisione e controllo Sigma Air Manager 4.0 interconnessa alla rete aziendale per un monitoraggio puntuale dei processi.
Approfondimento Tecnico: "Sistema di controllo per compressori industriali"
Sesta fase
Il monitoraggio di ogni singolo locale compressori e la registrazione delle principali variabili di riferimento hanno consentito di verificare il reale risparmio energetico, oltre alla contabilizzazione dell’efficienza specifica.
Grazie alla supervisione della sala compressori, è stato possibile implementare un “service preventivo e predittivo” che permetta di ridurre i costi manutentivi.
Approfondimento: " Tutto quello che devi sapere sulla Manutenzione Preventiva, Correttiva e 4.0"
L'ottenimento di risultati lusinghieri
Come in tutti i progetti, la parte di rendicontazione finale è quella che sancisce, rispettivamente, la valenza dell’approccio utilizzato, la bontà del lavoro fatto e dei prodotti selezionati e, conseguentemente, l’avere centrato l’obiettivo.
Nel caso in esame, approcciando in maniera “oggettiva” i numeri misurati prima e dopo l’attività di ottimizzazione, è stato possibile verificare che le valutazioni più ambiziose di risparmio energetico ottenibile con le nuove stazioni di aria compressa Kaeser sono state superate.
L’approccio e la metodologia utilizzata da Kaeser e dal Kaeser Point di riferimento, sia nello sviluppo di nuovi progetti che nell’ottimizzazione di stazioni esistenti, confermano ancora una volta di essere di fronte a Professionisti dell’Efficienza in grado di guidare i propri clienti attraverso le soluzioni più innovative ed efficaci, realizzando in ogni progetto un “abito su misura”.
Lascia un commento