Nell'industria, vi sono innumerevoli installazioni in cui gli impianti di aria compressa lavorano in maniera totalmente scoordinata. In queste installazioni, il rapporto tra l’aria prodotta dai compressori e l'aria effettivamente utilizzata è estremamente svantaggioso.
La richiesta di aria compressa può essere estremamente variabile, in funzione dei turni e delle condizioni di lavoro e, se la produzione di aria compressa non segue in modo affidabile l'effettiva richiesta, il risultato non può che essere un uso inefficiente dell'energia, specialmente a carichi parziali, con sprechi economici rilevanti per l'utilizzatore.
I costi di consumo di energia possono rappresentare fino all'87% dei costi annui legati all'aria compressa, in funzione del numero di ore di uso dei compressori.
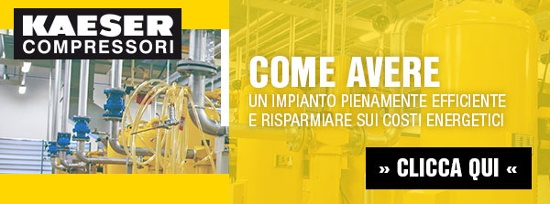
Un impianto di aria compressa efficiente?
Abbiamo visto che lavorare e forzare un impianto di aria compressa inefficiente ha come risultato che vengono generati elevati consumi di energia elettrica, bassa produttività e peggioramento delle prestazioni e degli strumenti che ricorrono all'utilizzo dell’aria.
Tubazioni più vecchie di 5 anni possono essere causa di perdite d'energia fino al 25%. Tuttavia, nonostante questo, molti impianti sono ancora poco reattivi nell’implementazione di interventi volti al miglioramento della struttura, in linea con soluzioni tecnologicamente più avanzate.
Inoltre, reti di distribuzione dell’aria compressa sotto o sovra dimensionate, sistemi progettati male o filtri intasati possono creare una domanda artificiale significativa.
Un primo livello di controllo e valutazione dell'efficienza dell'impianto aria compressa, consiste nel monitorare alcuni elementi principali quali:
- Basse cadute di pressione tra il compressore e il punto di utilizzo dell’aria compressa. (qui un utile strumento per il calcolo della caduta della pressione)
- Minime perdite dalle tubazioni.
- Separazione della condensa efficiente (qualora nel contesto analizzato non sia presente un essiccatore).
Un aspetto da tenere sempre in considerazione è dato dalla differenza di costo tra progettare l’impianto correttamente la prima volta e ricostruire l’intera rete di distribuzione in seguito.
E' inoltre, cosa molto intelligente cercare di ragionare in maniera proattiva ed adattiva, ovvero costruendo un impianto ed una rete di distribuzione dell'aria compressa adeguati alle esigenze nel presente, ma modulare al fine di poter essere ampliato o ridotto nel momento stesso in cui le esigenze o il contesto venissero a modificarsi nel corso del tempo.
Mediamente un quarto dell'aria compressa si disperde a causa di fughe. Così, si fa presto ad accumulare un importo annuo elevato per costi inutili.
Il risparmio energetico, a cui il mercato guarda con crescente interesse e sensibilità, orienta la scelta delle nuove installazioni verso compressori dotati di inverter proprio perchè, grazie a questa tipologia di impianto di aria compressa, è possibile consumare solo l’energia necessaria per produrre l’aria richiesta dall’impianto, senza sprechi. Una scelta così strutturata è orientata anche dalla frequente volatilità dei consumi che derivano a loro volta dalla variabilità del ritmo di produzione.
Va precisato però che l’applicazione di un inverter richiede una rilevazione strumentale sui consumi di aria compressa al fine di analizzare la convenienza e il tempo di ritorno dell’investimento dato che questa tipologia di impianti costa mediamente il 30% in più.
Per approfondire l'argomento leggi anche: " Compressore inverter: La soluzione per l'efficienza energetica aziendale "
Impianti aria compressa: come scegliere controller e compressore più adatto
I moderni costruttori offrono diverse possibilità di variare l'aria prodotta da un impianto di aria compressa per coprire al meglio la richiesta delle utenze, spaziando dai controller installati a bordo macchina fino ai master controller o air manager.
La domanda su quale tipo di controller e quale scelta di compressori sia corretta per una particolare applicazione, può avere un'adeguata risposta solo quando è nota con precisione la portata richiesta su un certo periodo. E' consigliabile non affidarsi a stime approssimative, ma misurare e calcolare con precisione l'effettivo consumo e il modo con cui questo viene soddisfatto, su un opportuno periodo lavorativo.
L‘uso dei controller di un impianto di aria compressa e dei sistemi di gestione centralizzati consente una produzione economica e ad alta efficienza energetica di aria compressa anche a condizioni di carico parziale, frazionando opportunamente il carico su un certo numero di compressori.
Per approfondire l'argomento leggi anche: "Portata volumetrica: misurazione del compressore volumetrico"
Frazionamento del carico di un impianto di aria compressa
Generalmente, esistono diverse possibilità di frazionamento del carico per numero e taglie di compressori.
Quando si fraziona il carico nei sistemi multi-compressore, la relazione fra le diverse portate dei compressori è estremamente importante per la corretta regolazione. La somma delle portate di almeno due compressori di picco di ugual taglia deve essere sempre maggiore della portata del compressore, di carico medio o base, immediatamente più grande.
Allo stesso modo, la somma delle portate di questi compressori deve essere di nuovo maggiore della portata del compressore successivo; questa regola deve essere applicata in modo iterativo.
Le tipologie dei sistemi di controllo per un impianto di aria compressa
Una volta dimensionato correttamente l'impianto di aria compressa, si passa alla scelta del sistema di controllo. Nel tempo, i sistemi centralizzati sono stati sempre più sviluppati e affinati.
Il più semplice e antico sistema è il controllo a cascata, che può essere realizzato anche senza un master controller, in quanto consiste nell'impostare su ciascun compressore le pressioni di attivazione e disattivazione, in modo opportunamente scalato, attribuendo così a ciascuna unità un ruolo di macchina di carico base, medio o di picco.
Un ulteriore sviluppo ottenuto tramite i master controller si è avuto facendo alternare i compressori di pari capacità in modo da bilanciare le ore di lavoro. All'aumentare della quantità di macchine, il campo di pressione totale aumenta comportando un aumento della pressione massima di lavoro del sistema.
Allo scopo di ridurre il più possibile la pressione di lavoro in stazioni con molti compressori, sono stati introdotti i controller a banda di pressione. Il principio di funzionamento consiste nell'attivare e disattivare le macchine all'interno di un predefinito range di pressione, in cui il gap compreso tra i limiti massimo e minimo è il più stretto possibile.
Il sistema è poi in grado di controllare un numero crescente di compressori mantenendo il limite impostato e quindi contenendo il valore massimo di pressione di esercizio.
Perché serve un master controller ad un impianto di aria compressa?
Le moderne stazioni d’aria compressa devono far fronte alle più svariate esigenze. Di solito in una stazione d’aria occorre l’azione concertata di più compressori e componenti per il trattamento dell’aria, prestando particolare attenzione alla sinergia dei compressori; gestendo i consumi di energia possiamo realizzare i maggiori risparmi.
Occorre quindi l’abilità di master controller intelligenti, capaci di coordinare ed armonizzare le singole unità, per conseguire l’obiettivo di un impianto ben regolato ed efficiente.
Il controllo a banda di pressione con set-point consente un ulteriore riduzione del campo di pressione di esercizio, tenendo conto della variazione all'interno di intervalli di tempo predefiniti, allo scadere dei quali le unità vengono commutate a carico o a vuoto.
Il più evoluto sistema oggi disponibile è il controllo adattivo che, oltre ad assicurare la minima pressione di esercizio possibile, permette di ottimizzare la quantità di commutazioni, allo scopo di ridurre i consumi di energia elettrica attraverso la limitazione delle perdite e l'impiego di energia nel funzionamento a vuoto.
Leggi anche: " Compressori Kaeser e Sigma air service: Assistenza e Know How "
La domanda energetica di un impianto di aria compressa ad alta efficienza è minimizzata tramite l'aggiustamento automatico delle condizioni di funzionamento attuali.
La selezione dei compressori da attivare e disattivare e le relative pressioni di commutazione sono di volta in volta determinate in funzione di diversi parametri, tra i quali il consumo di aria, lo stato di funzionamento delle unità, la potenza totale impegnata. La pressione di esercizio non scende mai al di sotto di un valore minimo specificato.
Lascia un commento